Polyethylene bottles are everywhere. From the soda you drink to the shampoo you use, these bottles are an essential part of our daily lives. They’re not just affordable, but also incredibly versatile. Whether you’re a manufacturer looking for cost-effective packaging or a consumer who needs something durable, polyethylene bottles have got you covered. Let’s explore why these bottles are such a popular choice.
Основные выводы
- Polyethylene bottles are a cost-effective packaging option, widely used across various industries.
- They are known for their durability and strength, making them ideal for everyday use.
- Polyethylene is recyclable, which helps in reducing environmental impact.
- These bottles are used in diverse sectors, including beverages, personal care, and industrial applications.
- Manufacturing involves techniques like blow molding and injection molding to ensure quality and efficiency.
Understanding Polyethylene Bottles
What Are Polyethylene Bottles?
Polyethylene bottles are a staple in packaging, serving as containers for everything from beverages to cleaning products. These bottles are made from polyethylene, a versatile plastic known for its durability and flexibility. Polyethylene is one of the most widely used plastics in the world, thanks to its adaptability and cost-effectiveness. It comes in various forms, mainly high-density polyethylene (HDPE) and low-density polyethylene (LDPE), each serving different purposes based on their properties.
History of Polyethylene Bottles
The journey of polyethylene bottles began in the early 20th century when polyethylene was first synthesized. However, it wasn’t until the 1950s that polyethylene bottles became popular, especially with the advent of blow molding techniques that allowed for mass production. This innovation made it possible to produce lightweight, durable bottles at an affordable price, revolutionizing the packaging industry.
Types of Polyethylene Used in Bottles
There are primarily two types of polyethylene used in bottle production:
- High-Density Polyethylene (HDPE): Known for its strength and rigidity, HDPE is often used in bottles that hold milk, juice, and household cleaners. It’s resistant to impact and chemicals, making it ideal for a variety of applications.
- Low-Density Polyethylene (LDPE): This type of polyethylene is more flexible and is commonly used for squeeze bottles, like those for condiments. LDPE is valued for its clarity and ease of processing.
Each type of polyethylene offers unique benefits, ensuring that manufacturers can choose the right material for their specific needs. The choice between HDPE and LDPE often depends on the desired balance between flexibility, strength, and clarity.
The development and use of polyethylene bottles have significantly influenced packaging, offering a reliable and economical solution for preserving and transporting a wide range of products.
Benefits of Using Polyethylene Bottles
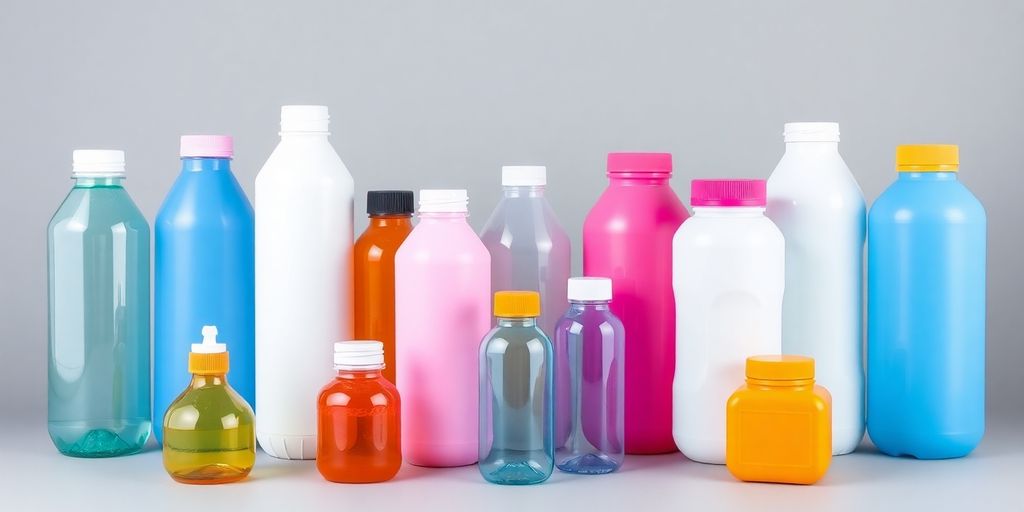
Cost-Effectiveness of Polyethylene Bottles
Polyethylene bottles are a hit in the packaging world mainly because they don’t break the bank. They’re super affordable to make and ship, which is a big deal for companies looking to cut costs. Imagine saving a chunk of change just by choosing the right bottle! Plus, these bottles are lightweight, making them cheaper to transport. It’s like getting more bang for your buck every time you ship out a batch.
Durability and Strength
When it comes to strength, polyethylene bottles are like the superheroes of the packaging world. They can take a hit without cracking, which is perfect for products that need to survive a bumpy ride. Whether they’re holding something fizzy or something fragile, these bottles are built to last. You don’t have to worry about them breaking easily, which is a relief for both manufacturers and consumers.
Environmental Impact and Recyclability
Here’s the thing about polyethylene bottles—they’re not just tough; they’re also kind to the planet. These bottles can be recycled over and over again, which is a huge plus for the environment. Recycling them helps reduce waste and saves resources, making them a smart choice for eco-conscious brands. It’s all about doing your part for the planet while still getting a reliable packaging solution.
Polyethylene bottles offer a blend of affordability, durability, and eco-friendliness that makes them a top choice in the packaging industry.
Applications of Polyethylene Bottles
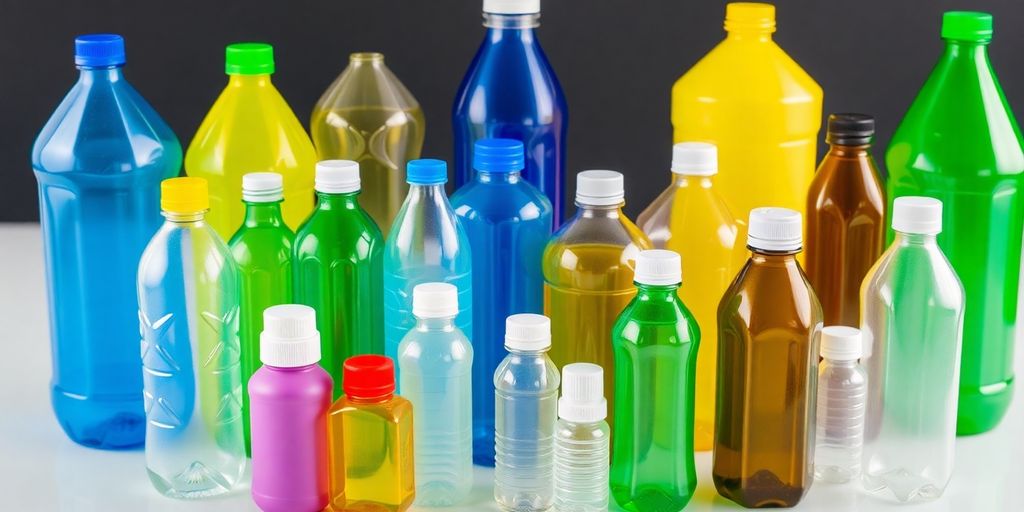
Polyethylene Bottles in the Beverage Industry
Polyethylene bottles have become a staple in the beverage industry. They are widely used for packaging a variety of drinks, from water and juices to sodas and even alcoholic beverages. Their lightweight nature and durability make them an ideal choice for manufacturers looking to reduce shipping costs and minimize breakage. Plus, these bottles can be easily molded into different shapes and sizes, allowing brands to create unique packaging that stands out on the shelves.
Use in Personal Care Products
When it comes to personal care products, polyethylene bottles are often chosen for their flexibility and resilience. Shampoos, conditioners, lotions, and creams are frequently packaged in these bottles because they can withstand the rigors of bathroom environments, such as moisture and temperature changes. Polyethylene is also popular for its ability to be easily colored or decorated, which is a big plus for brands wanting to make their products visually appealing.
Industrial Applications
In industrial settings, polyethylene bottles are used to store and transport a wide range of chemicals and other materials. Their chemical resistance and strength make them suitable for holding everything from cleaning agents to automotive fluids. Moreover, these bottles often come with specialized closures or dispensing systems, ensuring the safe and efficient use of the contents. The versatility of plastic containers extends to various applications, making them a reliable choice for many industries.
Manufacturing Process of Polyethylene Bottles
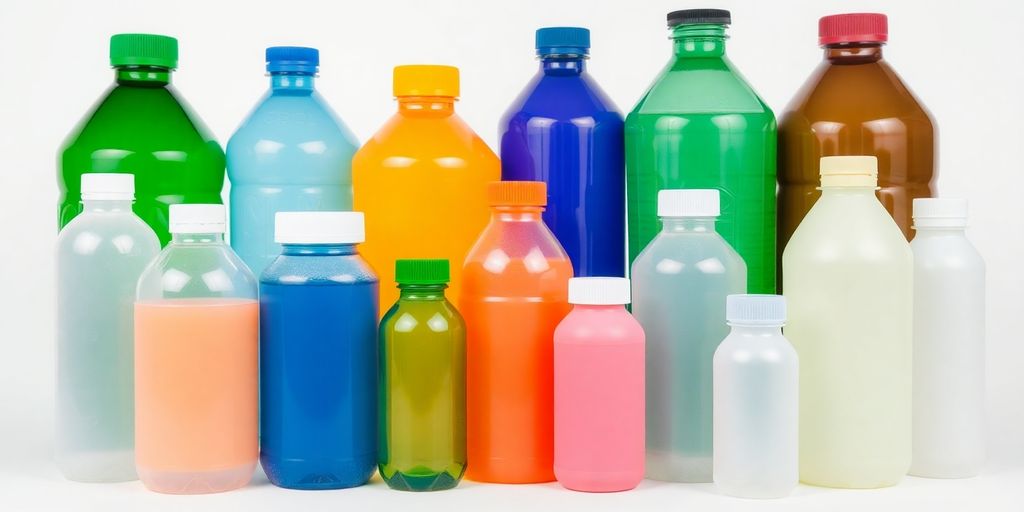
Creating polyethylene bottles is a fascinating journey from raw plastic to a finished product. The process involves several steps, each crucial to ensuring the bottles are durable, lightweight, and cost-effective. Let’s break down the manufacturing process into key stages.
Blow Molding Techniques
Blow molding is a popular method for shaping polyethylene into bottles. It involves inflating heated plastic into a mold cavity. Here’s a simple rundown of how it works:
- Extrusion: The polyethylene is melted and formed into a hollow tube known as a parison.
- Inflation: The parison is clamped into a mold and air is blown into it, inflating it into the shape of the mold.
- Cooling: The mold is cooled, solidifying the plastic into its final shape.
This technique is widely used because it allows for the production of complex shapes and sizes with minimal waste. For a deeper understanding, explore the blow molding process and its applications in various industries.
Injection Molding for Polyethylene Bottles
While blow molding is common, injection molding also plays a role in creating polyethylene bottles, especially for parts like caps and closures. Here’s how it works:
- Melting: Polyethylene pellets are melted in a heated barrel.
- Injection: The molten plastic is injected into a mold cavity.
- Cooling and Ejection: The plastic cools and hardens, then is ejected from the mold.
This method is precise, making it ideal for producing small, detailed components. Learn more about the polyethylene manufacturing process and how it incorporates various molding techniques.
Quality Control in Production
Ensuring quality in the production of polyethylene bottles is paramount. Manufacturers implement rigorous quality control measures, which include:
- Dimensional Checks: Ensuring the bottles meet specified dimensions.
- Visual Inspection: Checking for defects like bubbles or inconsistencies in the plastic.
- Pressure Testing: Ensuring the bottles can withstand internal pressure without leaking.
Quality control is essential to maintain consumer trust and meet industry standards. The environmental impact study on PET bottle production machines highlights the importance of efficiency and sustainability in manufacturing processes.
The journey of a polyethylene bottle from raw material to store shelf involves a blend of technology and precision. Each step in the manufacturing process is designed to deliver a product that meets the needs of both manufacturers and consumers.
Comparing Polyethylene Bottles with Other Materials
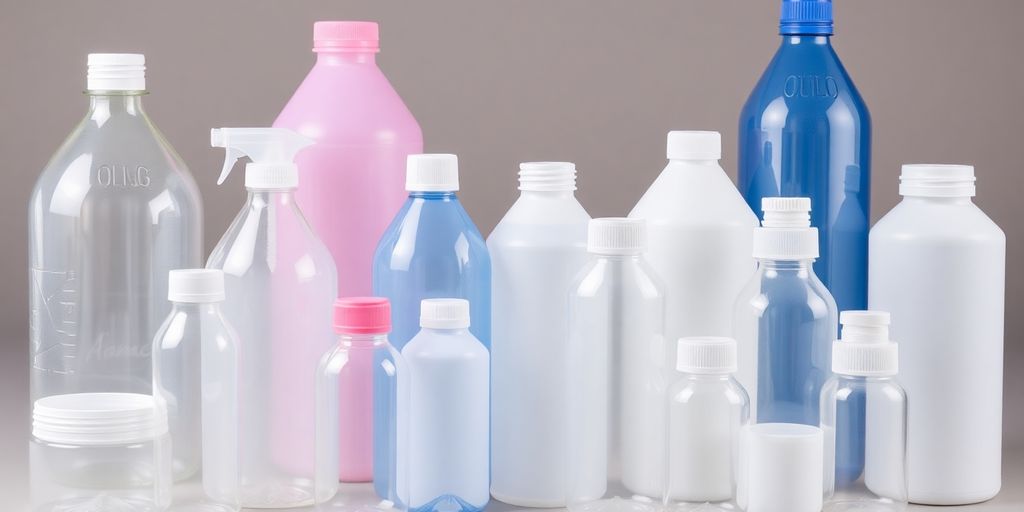
Polyethylene vs. Glass Bottles
When it comes to choosing between polyethylene and glass bottles, each has its own perks and drawbacks. Polyethylene bottles are lightweight and shatterproof, making them a safer option, especially for kids and outdoor activities. In contrast, glass bottles offer a premium feel and are often preferred for products where purity and taste are critical, like certain beverages. However, glass is heavier and more prone to breakage, which can increase shipping costs and risk of damage.
Характеристика | Polyethylene Bottles | Glass Bottles |
---|---|---|
Вес | Light | Heavy |
Долговечность | Shatterproof | Breakable |
Recyclability | Widely recyclable | Recyclable |
Стоимость | Generally cheaper | More expensive |
For more on how these materials compare in terms of sustainability and cost, check out this comparison of glass and plastic bottles.
Polyethylene vs. Metal Cans
Polyethylene bottles and metal cans are both popular in the packaging world, but they serve different needs. Polyethylene is flexible and can be molded into various shapes, which is great for branding. Metal cans, on the other hand, are excellent for preserving the freshness and carbonation of beverages. They also offer a sturdy barrier against light and oxygen, which is crucial for some products. Yet, cans can be heavier and not as versatile in shape as polyethylene bottles.
Advantages Over Other Plastics
Polyethylene stands out among other plastics like PET and PP due to its cost-effectiveness and versatility. It’s used widely because it’s easy to produce and recycle. Compared to PET, polyethylene might not always be as clear, but it’s often more durable. PET is favored for its clarity and ability to hold carbonated drinks, while polyethylene is often chosen for its resilience and lower cost. For a deeper dive into the benefits of PET and HDPE in bottling, particularly their lightweight nature, check out more detailed discussions.
Innovations in Polyethylene Bottle Design
Lightweight and Ergonomic Designs
Polyethylene bottles are evolving with a focus on making them lighter and more comfortable to handle. These designs help reduce material use and make transportation cheaper. By using less plastic, manufacturers not only cut costs but also help the environment. Ergonomic designs make bottles easier to grip, which is great for consumers, especially when pouring or carrying.
Customizable Shapes and Sizes
One of the coolest things about polyethylene bottles is how they can be molded into almost any shape or size. This flexibility lets brands create unique designs that stand out on store shelves. From sleek, modern shapes to classic styles, the possibilities are endless. Plus, having different sizes means they can cater to a wide range of customer needs, whether it’s a small bottle for travel or a large one for family use.
Advancements in Closure Technology
Closures are getting smarter and more efficient, too. Innovations in cap design ensure bottles remain sealed tightly, preventing leaks and keeping contents fresh. Some new closures even come with features like child-proofing or easy-open mechanisms. This is particularly important for products like medications or household cleaners, where safety is a big concern.
With the rise of Frugalpac’s mono material pouch, polyethylene bottles are seeing competition, but their ability to innovate keeps them relevant. As designs continue to evolve, these bottles remain a staple in packaging solutions for many industries.
Challenges and Solutions in Polyethylene Bottle Production
Addressing Environmental Concerns
Polyethylene bottles, while incredibly useful, pose significant environmental challenges. The production process is energy-intensive and contributes to pollution. Moreover, the disposal of these bottles often leads to environmental degradation. Efforts are being made to reduce the carbon footprint of polyethylene bottle production. Companies are increasingly investing in research to develop more sustainable production methods, such as using renewable energy sources and optimizing manufacturing processes.
Improving Recycling Processes
Recycling polyethylene bottles is another major hurdle. The limited quantity of collected plastic waste and the lower quality of recycled materials make it difficult to achieve effective recycling. To tackle this, advancements in recycling technology are crucial. Enhanced sorting techniques and better recycling facilities can improve the quality of recycled materials. Additionally, creating awareness about the importance of recycling can drive more consumer participation.
Overcoming Design Limitations
Designing polyethylene bottles that meet both consumer and environmental needs is a complex task. Bottles need to be durable, lightweight, and aesthetically pleasing, all while being environmentally friendly. Innovations in design, such as lightweight and ergonomic designs, are helping manufacturers meet these demands. By focusing on customizable shapes and sizes, and advancing closure technology, companies can create more efficient and appealing products.
The journey to more sustainable polyethylene bottle production is ongoing, with challenges still to be addressed. However, through innovation and commitment, progress is being made towards a more sustainable future.
In summary, while the production of polyethylene bottles faces several challenges, solutions are being developed and implemented. These efforts are crucial not just for the industry but for the environment as well.
Making polyethylene bottles comes with its own set of challenges, like managing costs and ensuring quality. However, there are effective solutions available, such as using better materials and improving production methods. If you’re interested in learning more about how we can help you overcome these challenges, visit our website today!
Заключение
Polyethylene bottles have proven themselves as a go-to choice for packaging, thanks to their affordability and versatility. They’re lightweight, which makes them easy to transport, and they’re tough enough to handle everyday use without breaking. Plus, with the ability to be recycled, they offer an eco-friendly option for businesses looking to reduce their environmental impact. Whether it’s for beverages, cleaning products, or personal care items, polyethylene bottles provide a reliable and practical solution. As more companies aim for sustainability, these bottles are likely to remain a staple in packaging for years to come.
Часто задаваемые вопросы
What are polyethylene bottles made of?
Polyethylene bottles are made from a type of plastic called polyethylene, which is known for being lightweight and durable.
Are polyethylene bottles safe for food and drinks?
Yes, polyethylene bottles are safe for packaging food and drinks. They are widely used for this purpose because they don’t react with the contents.
Can polyethylene bottles be recycled?
Absolutely! Polyethylene bottles can be recycled, which helps reduce waste and protect the environment.
How are polyethylene bottles different from PET bottles?
While both are types of plastic, polyethylene bottles are generally more flexible, whereas PET bottles are known for being clear and rigid.
What industries use polyethylene bottles?
Polyethylene bottles are used in various industries including beverages, personal care, and industrial sectors due to their versatility.
Why choose polyethylene bottles over glass or metal?
Polyethylene bottles are preferred for their lightweight, cost-effectiveness, and durability compared to glass or metal containers.