Sacar su producto a la calle y ponerlo en manos de los clientes es algo muy importante, ¿verdad? Pero antes hay que asegurarse de que todo está en perfecto estado. Ahí es donde entra en juego una lista de control de calidad. Es como una guía a la que acudir para detectar cualquier contratiempo antes de que se convierta en un problema en toda regla. Ya sea para asegurarse de que el embalaje es resistente o de que las etiquetas son las correctas, una lista de control sólida puede ahorrarle muchos quebraderos de cabeza. Veamos por qué es innegociable tener una lista de control y qué debe incluir para que todo vaya sobre ruedas.
Principales conclusiones
- Una lista de control de calidad es esencial para detectar problemas antes de que los productos salgan al mercado.
- Ayuda a garantizar que el envasado y el etiquetado del producto cumplen todas las normas necesarias.
- Formar a su equipo en la lista de comprobación puede aumentar la eficacia y reducir los errores.
- Las actualizaciones periódicas de la lista de control mantienen su pertinencia y eficacia.
- Superar los retos que plantean los procesos de control de calidad es crucial para que la calidad del producto sea constante.
Comprender la importancia de una lista de control de calidad
Definición de una lista de control de calidad
Una lista de control de calidad (CC) es una guía detallada que describe los criterios y procedimientos específicos para inspeccionar un producto antes de que salga al mercado. Este documento es crucial para recogida y análisis sistemáticos de datos sobre la calidad de los productos durante la producción, garantizando que cada artículo cumple las normas predefinidas. Con una lista de control de calidad, las empresas pueden asegurarse de que las comprobaciones son minuciosas y coherentes, lo que reduce el riesgo de que se escapen defectos.
Ventajas de utilizar una lista de control de calidad
La aplicación de una lista de control de calidad ofrece varias ventajas:
- Consistencia en la calidad: Con una lista de control estándar, todos los productos se someten a los mismos rigurosos controles, lo que garantiza la uniformidad de los lotes.
- Identificación precoz de defectos: Las listas de comprobación ayudan a detectar problemas en una fase temprana del proceso de producción, lo que permite corregirlos a tiempo.
- Mejora de la comunicación: Una lista de comprobación clara facilita una mejor comunicación entre los equipos de producción y los inspectores de calidad, alineando a todos en torno a las mismas expectativas de calidad.
Errores comunes sobre las listas de control de calidad
A pesar de su importancia, existen varios conceptos erróneos sobre las listas de control de calidad:
- Talla única: Muchos creen que una única lista de comprobación puede servir para todos los productos e industrias, pero en realidad las listas de comprobación deben personalizarse para adaptarse a los requisitos específicos de cada producto.
- Demasiado tiempo: Algunos argumentan que el uso de una lista de comprobación ralentiza la producción. Sin embargo, invertir tiempo en comprobaciones de calidad puede ahorrar más tiempo y recursos a largo plazo al evitar costosas retiradas y repeticiones.
- Redundante para productos establecidos: Incluso los productos bien establecidos pueden beneficiarse de una lista de control de calidad para mantener la calidad a lo largo del tiempo y adaptarse a cualquier cambio en los métodos de producción o los materiales.
Componentes clave de una lista de control de calidad eficaz
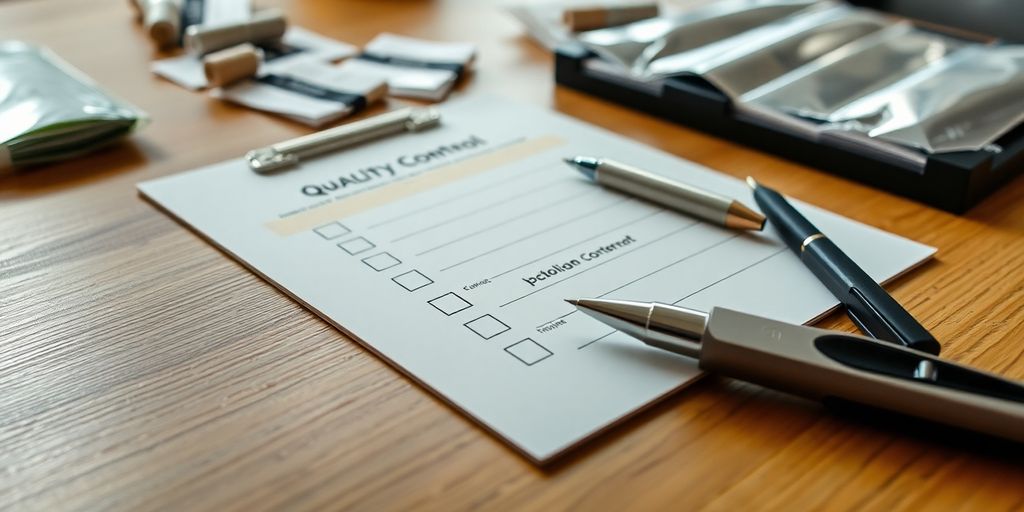
Especificaciones de productos y normas
Cuando se elabora una lista de control de calidad, lo primero que hay que tener en cuenta son las especificaciones y normas del producto. Se trata de la esencia de su producto. Hay que asegurarse de que todos los artículos que salen de la línea coinciden con el tamaño, el peso, el color y la funcionalidad prometidos. Esta es su línea de base de calidad.
- Tamaño y peso: Asegurarse de que los productos entran dentro de la gama aceptable.
- Consistencia del color: Compruebe que el color coincide con la muestra aprobada.
- Pruebas de funcionalidad: Compruebe que el producto cumple las funciones previstas.
Requisitos de envasado y etiquetado
Lo siguiente es el envasado y etiquetado. No se trata solo de poner una etiqueta en una caja. Se trata de asegurarse de que el producto llega sano y salvo y tiene buen aspecto. Un embalaje adecuado evita daños y garantiza la satisfacción del cliente.
- Calidad del material: Utilice materiales duraderos para proteger el producto.
- Precisión de las etiquetas: Asegúrese de que las etiquetas contienen la información correcta y son legibles.
- Cumplimiento de las normas de seguridad: Siga las normas del sector en materia de envasado.
Cumplimiento y controles reglamentarios
Por último, no olvide los controles de conformidad y reglamentarios. Son las reglas del juego. Debe asegurarse de que su producto cumple todas las normas legales y del sector. No cumplirlas puede acarrear multas o retiradas del mercado.
- Normas reglamentarias: Confirme que el producto cumple todos los requisitos legales necesarios.
- Documentación: Mantener registros de todos los controles de conformidad.
- Protocolos de ensayo: Seguir los procedimientos establecidos para garantizar el cumplimiento.
Pasos para elaborar una lista de control de calidad exhaustiva
Identificación de puntos críticos de control
Creación de una Lista de control de calidad empieza por identificar los puntos críticos de control en su proceso de producción. Son las fases en las que pueden surgir posibles problemas de calidad, y necesitan una estrecha vigilancia. Piense en ellos como la columna vertebral de sus esfuerzos de garantía de calidad. Para identificar estos puntos, colabore con su equipo y con inspectores de calidad externos. A partir de experiencias anteriores, pueden aportar información sobre lo que requiere más atención.
Incorporación de las normas del sector
Es fundamental incorporar las normas del sector a su lista de comprobación. Esto garantiza que sus productos cumplen los requisitos básicos que se esperan en su campo. Investigue e incluya las normas pertinentes, ya sean de seguridad, impacto ambiental o especificaciones técnicas concretas. Este paso no sólo ayuda a mantener la calidad, sino también a desarrollar un marco sólido de garantía de la calidad.
Personalización de productos específicos
Cada producto es único, y también debería serlo su lista de control de calidad. Personalice su lista de comprobación para responder a las necesidades y características específicas de su producto. Tenga en cuenta factores como las especificaciones de los materiales, las tolerancias de diseño y la funcionalidad. Adapte su lista de comprobación para reflejar estos atributos únicos, asegurándose de que cada producto se evalúa según su propio conjunto de criterios. Esta personalización ayuda a satisfacer las demandas de nichos de mercado y a mantener un alto nivel de exigencia.
Formación de su equipo en la aplicación de la lista de control de calidad
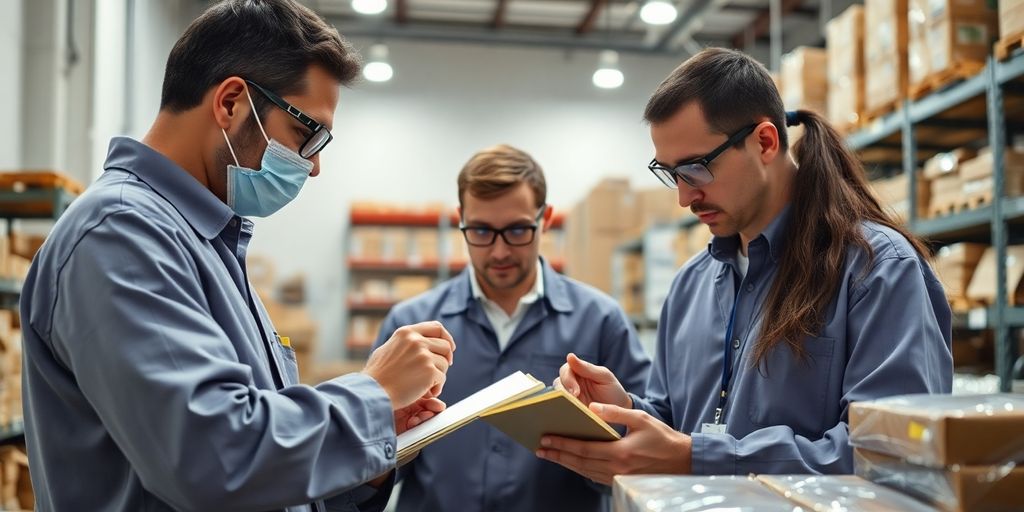
Importancia de la formación en equipo
Formar a su equipo en el uso de una lista de control de calidad es como enseñarles las reglas de un nuevo juego. Es fundamental que entiendan todas las reglas y estrategias para jugar con eficacia. Sin una formación adecuada, su equipo podría no dar en el clavo en el control de calidad, lo que podría provocar defectos en los productos o problemas de conformidad. Piénselo: un equipo bien formado puede detectar posibles problemas antes de que se conviertan en costosos errores. En sectores con normativas estrictas, como el manufacturero, un equipo bien formado puede detectar posibles problemas antes de que se conviertan en costosos errores. lista de control de la formación integral de los empleados puede agilizar las operaciones y mejorar la seguridad. Por eso, invertir tiempo en formación es rentable a largo plazo.
Métodos para una formación eficaz
Para que su equipo se ponga al día, considere estos métodos de formación:
- Talleres prácticos: Esto permite a los miembros del equipo practicar el uso de la lista de comprobación en situaciones reales. Es una forma estupenda de aprender con la práctica.
- Sesiones de juegos de rol: Simule inspecciones de control de calidad para que su equipo se sienta cómodo con el proceso.
- Módulos de formación en línea: Utilice recursos digitales para flexibilizar los horarios de aprendizaje. Esto puede ser especialmente útil para los equipos remotos.
Cada método tiene sus ventajas, y combinarlos puede cubrir todas las bases. Por ejemplo, las listas de comprobación digitales pueden agilizar las tareas rutinarias, ayudando a su equipo a centrarse en mejorar el menú u otras áreas clave.
Mecanismos de seguimiento y retroalimentación
Una vez que la formación está en marcha, es importante vigilar cómo van las cosas. Establezca un sistema para supervisar el rendimiento y recoger opiniones. Por ejemplo:
- Revisiones periódicas: Programe reuniones breves para debatir los avances y abordar cualquier problema.
- Formularios de opinión: Permita que los miembros del equipo compartan sus opiniones sobre el proceso de formación.
- Métricas de rendimiento: Realice un seguimiento de los indicadores clave para medir la eficacia de la formación.
El feedback te ayuda a afinar el proceso de entrenamiento y a hacer los ajustes necesarios. Es como afinar un instrumento para conseguir el sonido perfecto. Además, incorporar los comentarios de las inspecciones puede conducir a una mejora continua de los procesos de control de calidad, como se ve en un Programa de formación en control de calidad. Esto garantiza que su equipo no sólo esté formado, sino que también confíe en ejecutar sus tareas con eficacia.
Mejora continua de los procesos de control de calidad
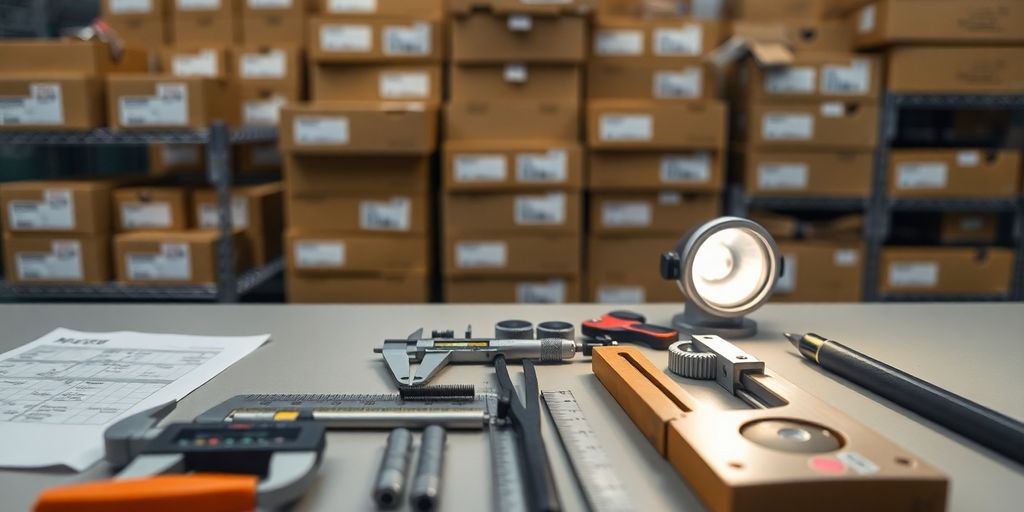
Revisión y actualización de la lista de control
Para mantener su procesos de mejora continua eficaz, tienes que comprobar y ajustar regularmente tu lista de control de calidad. No se trata de "ponerla y olvidarla". Cada vez que se lanza un nuevo producto o se modifican los materiales, la lista de control debe reflejar esos cambios. Las revisiones periódicas ayudan a detectar las deficiencias de la lista de comprobación. Si algo no detecta un defecto, es hora de hacer ajustes. Esta revisión continua ayuda a garantizar que la lista de control siga siendo una herramienta útil para mantener la calidad.
Incorporación de los resultados de las inspecciones
Los comentarios son oro. Después de las inspecciones, recabe la opinión de la gente sobre el terreno. Ellos saben lo que funciona y lo que no. Anímeles a compartir sus ideas sobre cómo mejorar el proceso. De este modo, no sólo mejorará la lista de control, sino que su equipo se sentirá valorado y escuchado. Esto puede conducir a un mayor compromiso y apropiación del proceso. Escuchar a quienes utilizan la lista de comprobación a diario puede descubrir problemas que podrían no ser obvios a un nivel superior.
Aprovechar la tecnología para mejorar el control de calidad
En el mundo tecnológico actual, el uso de la tecnología puede impulsar sus esfuerzos de control de calidad. Herramientas como las listas de comprobación digitales y los sistemas automatizados pueden agilizar el proceso, haciéndolo más eficaz y menos propenso a errores humanos. Considere la posibilidad de integrar Gestión de la calidad total para alinear sus procesos de control de calidad con objetivos organizativos más amplios. La tecnología también puede proporcionar análisis que ayudan a identificar tendencias y áreas que necesitan mejoras, garantizando que sus procesos de CC estén siempre actualizados y sean eficaces.
Desafíos comunes en la ejecución de la lista de control de calidad

Vencer la resistencia al cambio
A menudo, la implantación de una nueva lista de control de calidad se topa con la resistencia de los miembros del equipo, acostumbrados a las viejas formas de hacer las cosas. El cambio es duro, y la gente se resiste a él por naturaleza. Para solucionarlo, implique a su equipo en las primeras fases del proceso. Explíqueles claramente las ventajas, por ejemplo, cómo una lista de comprobación puede agilizar su trabajo y reducir los errores. A veces, mostrarles cómo la lista de comprobación mejora sus tareas diarias puede suponer una gran diferencia.
Garantizar la coherencia entre los equipos
Poner a todo el mundo de acuerdo es complicado, sobre todo si los equipos están repartidos por distintos lugares. Es crucial contar con un lista de control de calidad que esté estandarizada, pero que también sea lo bastante flexible para adaptarse a las necesidades locales. Las sesiones de formación periódicas y los circuitos de retroalimentación pueden ayudar a mantener la uniformidad. Utilice herramientas digitales para mantener la lista de comprobación accesible y actualizada para todos los equipos, garantizando que todos sigan los mismos procedimientos.
Recursos limitados
Los recursos pueden ser un obstáculo importante. Ya sea por falta de tiempo, personal o equipos, estas limitaciones pueden afectar a la eficacia de su lista de control de calidad. Priorice los componentes más críticos de la lista de comprobación para aprovechar al máximo los recursos disponibles. Considere la posibilidad de invertir en automatización siempre que sea posible para aliviar algunas de estas presiones. Y recuerde que, a veces, una lista de comprobación sencilla y bien ejecutada es mejor que una compleja que nadie utiliza.
Implantar una lista de control de calidad no consiste sólo en marcar casillas, sino en crear una cultura en la que la calidad sea una responsabilidad compartida. Si aborda estos retos de frente, podrá fomentar un entorno en el que el control de calidad forme parte integral del flujo de trabajo.
Al abordar estos retos, no sólo mejorará el proceso de control de calidad, sino que también aumentará la eficacia y fiabilidad generales de sus operaciones.
Casos prácticos: Implantación con éxito de listas de control de calidad
En el mundo de la fabricación, Empresa A saltó a los titulares al reducir los defectos en 30% simplemente utilizando una sólida lista de comprobación de inspección de materiales entrantes. No fue casualidad. Se centraron en comprobaciones detalladas al principio, asegurándose de que las materias primas estaban en perfecto estado. Este enfoque proactivo ayudó a detectar problemas antes de que se convirtieran en problemas mayores.
Casos de éxito en el sector minorista
Los minoristas no son ajenos a los retos del control de calidad. Un fabricante de juguetes, por ejemplo, experimentó una notable mejora de la calidad de la producción con la implantación de un sistema de control de calidad. lista exhaustiva de control de calidad. Se centraron en la uniformidad del color y la calidad general, lo que dio sus frutos. Los clientes notaron la diferencia, y también sus cifras de ventas. Es un caso clásico de cómo la atención al detalle en el control de calidad puede aumentar realmente el atractivo de un producto en el mercado.
Innovaciones en las prácticas de control de calidad
En todos los sectores, la innovación es clave. El Departamento de Cuaderno de prácticas 5-S presenta diez estudios de casos en los que las prácticas 5S mejoraron la eficiencia en los sectores manufacturero, de servicios y público. Estas historias ponen de relieve cómo la adopción de prácticas estructuradas de control de calidad puede transformar las operaciones, haciéndolas más eficientes y fiables.
Cuando las empresas adoptan el control de calidad no como una casilla de verificación, sino como una parte esencial de sus operaciones, a menudo descubren que da lugar a productos mejores y clientes más satisfechos. Se trata de hacer del control de calidad una parte integral de la cultura, no solo una tarea que hay que realizar.
En nuestro "Casos prácticos: Implantación con éxito de listas de control de calidad" mostramos ejemplos reales de cómo las empresas han mejorado sus procesos de control de calidad. Estas historias ponen de relieve los cambios positivos que se derivan del uso de listas de comprobación eficaces. ¿Quiere saber más sobre cómo podemos ayudar a su empresa a tener éxito? Visite nuestro sitio web hoy mismo.
Para terminar
Ya hemos hablado mucho de las listas de control de calidad y de por qué son importantes. No se trata sólo de marcar casillas, sino de asegurarse de que lo que se envía es de primera calidad. Desde comprobar el aspecto del producto hasta asegurarse de que el envase es perfecto, cada paso cuenta. Y no hay que olvidar el papeleo, que es igual de importante. Al fin y al cabo, una buena lista de control de calidad es como una red de seguridad. Ayuda a detectar errores antes de que se conviertan en problemas. Así que tómese su tiempo para hacerlo bien. Sus clientes se lo agradecerán y su marca destacará por las razones adecuadas.
Preguntas frecuentes
¿Qué es una lista de control de calidad?
Una lista de control de calidad es una herramienta utilizada para garantizar que los productos cumplen las normas de calidad antes de ser enviados. Incluye directrices sobre el aspecto del producto, el envasado y las comprobaciones de conformidad.
¿Por qué es importante una lista de control de calidad?
Una lista de control de calidad ayuda a detectar defectos, garantiza que los productos cumplen las normas y mejora la satisfacción del cliente al ofrecer productos de alta calidad.
¿Cómo puedo crear una lista de control de calidad?
Para crear una lista de control de calidad, identifique los puntos críticos del proceso de producción, establezca normas de calidad y adáptela a las necesidades de su producto.
¿Qué debe incluir una lista de control de calidad?
Una lista de control de calidad debe incluir las especificaciones del producto, los requisitos de envasado, el etiquetado y los controles de conformidad para garantizar que todo cumple las normas establecidas.
¿Con qué frecuencia debe actualizarse una lista de control de calidad?
Una lista de control de calidad debe revisarse y actualizarse periódicamente, sobre todo cuando se produzcan cambios en el diseño del producto, los materiales o la normativa.
¿Cuáles son algunos de los retos que plantea el uso de una lista de control de calidad?
Entre los retos figuran la resistencia al cambio, garantizar la coherencia y hacer frente a las limitaciones de recursos, pero una formación adecuada y actualizaciones periódicas pueden ayudar a superarlos.